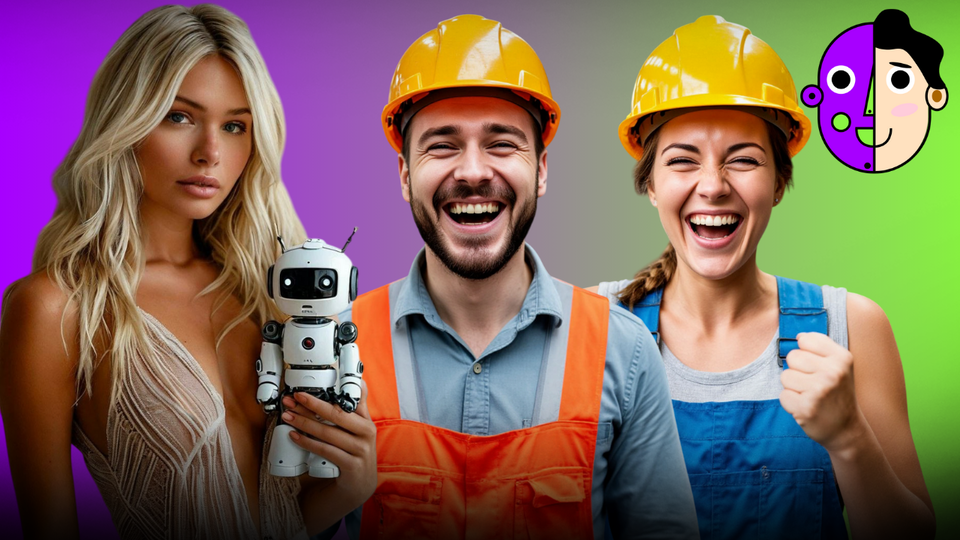
L’IA dans l’industrie : casques intelligents, inspecteurs quadrupèdes, jumeaux numériques
Au cœur de l’intelligence artificielle industrielle se trouveront des systèmes de maintenance prédictive pour l’analyse des équipements en temps réel. Ces solutions réduiront les temps d’arrêt non planifiés de quarante-cinq pour cent et augmenteront la durée de vie des actifs industriels de trente pour cent. Les systèmes cognitifs traiteront les données de milliers de capteurs, identifiant des modèles au-delà des capacités d’analyse humaine.
Pour les ingénieurs et les spécialistes industriels, cela implique de développer des compétences hybrides à l’intersection des connaissances industrielles et de la compréhension des capacités de l’intelligence artificielle. L’ingénieur du futur sera un interprète entre les algorithmes et le monde physique de la production.
Maintenant, je vais vous montrer des exemples reliant une industrie aussi vaste et développée que la fabrication avec une nouvelle technologie – l’intelligence artificielle.
Assemblage et démontage d’électronique complexe
Bright Machines a développé une solution complète transformant le processus d’assemblage et de démontage automatisés d’électronique complexe grâce à une combinaison unique de robotique intelligente, de logiciels basés sur l’intelligence artificielle et d’analyse de données.
La navigation tridimensionnelle utilise des modèles de vision en deux et trois dimensions, des métadonnées de produits et des capteurs de force pour déterminer l’orientation des pièces. Elle atteint une précision d’assemblage au niveau du micron et jusqu’à quatre-vingt-dix-huit pour cent de réussite au premier passage. Le système d’inspection visuelle automatisé, basé sur les mêmes technologies Smart Skills, vérifie les composants avant et après l’assemblage. Il identifie les anomalies, vérifie la présence des composants et détecte les traces d’accès non autorisés avec une extrême précision. Cela nécessite moins de mille échantillons pour entraîner les modèles d’apprentissage automatique.
Selon les analystes, le marché du matériel d’intelligence artificielle passera de trente-huit milliards de dollars en vingt-quatre à cent milliards d’ici vingt-sept. Parallèlement, les approches traditionnelles d’automatisation de l’assemblage démontrent une inflexibilité critique. La reconfiguration d’une ligne de production pour un nouveau produit prend en moyenne de quatre à seize semaines. La programmation initiale des robots industriels nécessite des mois de travail par des ingénieurs hautement qualifiés. Le travail humain reste le fondement de l’assemblage des serveurs et autres électroniques complexes. Cela conduit à des problèmes persistants de qualité difficiles à contrôler et à documenter. Les recherches montrent que jusqu’à soixante-dix pour cent des défauts dans l’assemblage des systèmes de serveurs sont liés à des facteurs humains : fatigue, incohérence des actions et contrôle subjectif. Avec une pénurie mondiale de spécialistes techniques qualifiés et une pression croissante sur les chaînes d’approvisionnement, cette situation crée un obstacle fondamental à la mise à l’échelle de la production d’infrastructures d’intelligence artificielle critiques.
Les technologies Bright Machines trouvent des applications dans divers aspects de l’assemblage des serveurs et d’autres électroniques. Le système d’intégration GPU extrait automatiquement les modules GPU lourds directement de l’emballage d’origine. Il les aligne et les installe dans le serveur, les fixe avec des vis à couple constant, enregistrant toutes les données pertinentes sur les pièces et les processus. Ces solutions démontrent des résultats impressionnants. L’introduction de nouveaux produits est accélérée vingt-huit fois par rapport aux méthodes traditionnelles. Elle permet la configuration d’une ligne de production pour un nouveau serveur en moins de quatre heures au lieu des semaines habituelles. La plateforme permet de produire plus de cinquante modèles différents sur la même ligne de production. Elle assure une traçabilité à cent pour cent de chaque composant et opération. Dans la fabrication circulaire, les solutions pour le tri, le ré-étiquetage et le test des modules DIMM accélèrent le traitement par sept.
L’automatisation des opérations monotones et physiquement exigeantes comme l’installation de dissipateurs thermiques ou la manipulation de GPU lourds réduit potentiellement le risque de maladies professionnelles et de blessures parmi les travailleurs. Selon les études ergonomiques, jusqu’à trente pour cent des travailleurs en fabrication souffrent de blessures dues aux mouvements répétitifs associées aux opérations d’assemblage monotones. Cela rend l’automatisation de ces tâches socialement significative. Cependant, cette même automatisation transforme inévitablement la structure de l’emploi. Elle déplace la demande du travail manuel peu qualifié vers des rôles hautement qualifiés dans la maintenance et la programmation des systèmes automatisés. La question clé concerne le rythme de cette transformation et la préparation de la société à la reconversion de la main-d’œuvre.
Fabrication de soudage
Imaginez une installation de production moderne où chaque soudure doit être parfaite, mais les soudeurs qualifiés sont en pénurie critique. Ce problème brise littéralement les chaînes de production dans le monde entier.
Path Robotics propose une approche révolutionnaire qui peut être qualifiée de véritable percée dans la fabrication de soudage. Leurs systèmes robotiques utilisent la vision par ordinateur, la numérisation tridimensionnelle et l’intelligence artificielle pour le soudage autonome sans programmeurs ni soudeurs.
Le soudage est un art qui nécessite des années de formation. Le déclin démographique a conduit les maîtres expérimentés à prendre leur retraite plus rapidement que n’arrivent les nouvelles générations. Dans certaines industries, la pénurie de soudeurs qualifiés atteint soixante-dix pour cent. Les erreurs dans les joints soudés peuvent coûter des millions de dollars, voire des vies humaines. La robotisation traditionnelle nécessite des investissements en capital coûteux et l’embauche de programmeurs. Cela la rend inaccessible à de nombreuses entreprises. Même les systèmes robotiques ne peuvent souvent pas s’adapter à la diversité des pièces et des conditions de soudage.
L’essence de la technologie réside dans un processus en trois étapes. D’abord, le système scanne la pièce et crée son modèle tridimensionnel. Ensuite, il analyse les données obtenues, comprenant les caractéristiques individuelles de chaque pièce. Enfin, il effectue le soudage de manière autonome, s’adaptant aux changements pendant l’opération. Des capteurs spécialement développés peuvent voir même les surfaces très réfléchissantes et résister aux conditions difficiles de l’environnement de production. Il est important de noter que Path Robotics propose un modèle “Robots en tant que service”. Cela permet aux entreprises de mettre en œuvre des technologies avancées sans dépenses en capital importantes. Cela change complètement l’économie de l’automatisation de la production, la rendant accessible même aux petites et moyennes entreprises.
La gamme de produits de l’entreprise comprend deux types principaux de robots : AF un, capable d’assembler et de souder de manière autonome de petites pièces, et AW trois – un véritable cheval de bataille pour les grands projets. Il est capable de produire des kilomètres de soudures parfaites avec une supervision minimale. Le marché des robots de soudage connaît une croissance exponentielle. Path Robotics occupe une niche unique grâce à son approche basée sur l’intelligence artificielle et l’autonomie.
La mise en œuvre des technologies Path Robotics permet aux entreprises d’augmenter considérablement la productivité et la qualité des opérations de soudage. Elle résout également le problème de pénurie de main-d’œuvre qualifiée. Les systèmes de l’entreprise ne nécessitent ni programmeurs, ni soudeurs, ni ajusteurs. Cela réduit considérablement les dépenses opérationnelles et élimine la dépendance vis-à-vis des spécialistes rares. Grâce au modèle “Robots en tant que service”, les entreprises peuvent commencer à utiliser des technologies de soudage avancées sans investissements initiaux importants. C’est particulièrement important dans des conditions d’incertitude économique. Les robots autonomes de Path peuvent fonctionner vingt-quatre heures sur vingt-quatre. Ils fournissent des soudures de qualité constamment élevée et minimisent le besoin de reprise. Selon l’entreprise, leurs systèmes réduisent considérablement le temps de cycle de production. Dans certains cas, ils permettent d’augmenter le volume de production de trois à quatre fois tout en améliorant la qualité et en réduisant les défauts.
Inspection d’équipements dans des conditions extrêmes
Imaginez une immense raffinerie de pétrole ou une usine chimique où des centaines d’unités d’équipement nécessitent une inspection régulière dans des conditions dangereuses pour les humains. Chaque année, des milliers de travailleurs sont blessés lors d’inspections de routine dans des zones industrielles à haut niveau de risque.
ANYbotics a développé une solution unique pour ces problèmes : le robot quadrupède autonome ANYmal. Grâce à son système de mouvement à quatre pattes unique basé sur l’apprentissage par renforcement, le robot peut manœuvrer dans des installations industrielles complexes à plusieurs niveaux. Il surmonte des obstacles inaccessibles aux robots à roues ou à chenilles. ANYmal est équipé d’un complexe de capteurs de haute technologie. Cela inclut des imageurs thermiques, des analyseurs de gaz, des lidars et des caméras à haute résolution pour collecter diverses données sur l’état des équipements. Le système utilise l’intelligence artificielle avancée et l’informatique de pointe pour traiter les informations directement à bord, sans besoin de connexion Internet constante.
Selon les recherches industrielles, les temps d’arrêt non planifiés des équipements coûtent aux entreprises industrielles des millions de dollars quotidiennement. Quatre-vingts pour cent des accidents auraient pu être évités grâce à une détection précoce des dysfonctionnements. Parallèlement, les méthodes d’inspection traditionnelles nécessitent beaucoup de temps et de ressources. Elles sont souvent incohérentes en raison de facteurs humains et ne peuvent pas fournir une surveillance régulière dans des zones difficiles d’accès ou dangereuses. En conséquence, les équipements critiques sont souvent vérifiés moins fréquemment que nécessaire pour un fonctionnement et une sécurité optimaux.
Le robot ANYmal planifie entièrement de manière autonome des routes optimales dans toute l’installation. Il détermine avec précision sa position à l’aide du logiciel Pharos pour la localisation et la cartographie simultanées. Il retourne de manière indépendante à la station de charge après avoir terminé sa mission. Il est important de noter que le système est certifié pour la sécurité. Cela lui permet d’être utilisé même dans des environnements explosifs.
ANYbotics a été fondée en seize en tant que spin-off de l’Institut fédéral suisse de technologie de Zurich. L’entreprise possède plus de quinze ans d’expérience en robotique autonome. Aujourd’hui, ANYbotics occupe des positions de leader dans le développement de robots mobiles pour des applications industrielles.
Les robots peuvent détecter les dysfonctionnements des équipements à un stade précoce. Cela permet de prendre des mesures préventives pour éviter les pannes coûteuses et les temps d’arrêt. L’imagerie thermique aide à détecter des anomalies invisibles à l’œil pendant le fonctionnement. La surveillance en temps réel des concentrations de gaz inflammables et toxiques permet aux opérateurs de prendre des précautions en temps opportun. De plus, les robots effectuent une numérisation tridimensionnelle des objets lors des inspections. Cela aide à maintenir à jour les jumeaux numériques de l’installation. Grâce à l’interface intuitive ANYmal Workforce, même les non-spécialistes peuvent facilement configurer des missions et gérer des robots. L’entreprise propose un modèle de Robot en tant que service. Cela permet aux entreprises de mettre en œuvre la robotique sans investissements en capital importants et d’étendre son application selon les besoins.
À l’avenir, nous pouvons nous attendre à l’intégration d’algorithmes d’intelligence artificielle plus avancés pour l’analyse prédictive. Cela permettra de prédire les pannes d’équipement possibles des semaines, voire des mois avant qu’elles ne se produisent.
Exécution de tâches répétitives
Environ quarante pour cent du temps de travail des employés est consacré à des tâches répétitives qui ne nécessitent ni réflexion créative ni prise de décisions complexes.
Rethink Robotics a développé sa propre approche de l’automatisation en créant une famille de robots collaboratifs qui travaillent en toute sécurité aux côtés des humains. Leur produit phare est le robot Reacher. Il incarne une nouvelle compréhension de la collaboration homme-machine.
Mais l’automatisation industrielle traditionnelle s’avère souvent trop coûteuse et inflexible pour les petites et moyennes entreprises. Elle nécessite des coûts de programmation importants et ne fournit pas d’interaction sûre avec les humains. En conséquence, un énorme potentiel de travail humain est dépensé pour des tâches qui pourraient être automatisées. Les entreprises perdent en compétitivité dans des conditions de demandes croissantes de flexibilité de production.
Grâce à des algorithmes d’intelligence artificielle avancés et une interface intuitive, Reacher peut être configuré pour effectuer des tâches complexes sans programmation. La formation prend moins de dix minutes même pour les utilisateurs sans préparation spéciale. Le robot offre une répétabilité de positionnement avec une précision jusqu’à plus ou moins zéro virgule zéro trois millimètres. Cela lui permet d’effectuer les opérations les plus délicates avec une confiance absolue. Le système de sécurité de Reacher est basé sur la détection de collision avec un effort minimal. Cela crée un environnement de travail fiable et sûr lors de l’interaction avec les humains. Pour les tâches logistiques, l’entreprise propose le robot autonome Ryder. Il se déplace de manière indépendante dans l’entreprise sans nécessiter de composants d’infrastructure supplémentaires. Son système sensoriel avancé avec une vue circulaire de trois cent soixante degrés assure une détection fiable des humains et un fonctionnement sûr.
La mise en œuvre des solutions Rethink Robotics apporte de nombreux avantages aux productions. Elle permet la création d’une main-d’œuvre intégrée combinant des robots formables, sûrs et rentables avec un travail humain qualifié. Cela devient effectivement un multiplicateur de main-d’œuvre qui optimise les coûts de main-d’œuvre. Les employés sont libérés des tâches sales, dangereuses et monotones. Cela leur permet de se concentrer sur un travail nécessitant une réflexion créative et une prise de décision. Grâce à la facilité de configuration et à l’interface intuitive, les robots peuvent être rapidement reconfigurés pour effectuer diverses tâches. C’est particulièrement important dans l’économie actuelle qui exige une flexibilité de production. Les robots Reacher avec diverses capacités de levage de sept à trente kilogrammes conviennent à un large éventail de tâches. Ils peuvent manipuler délicatement des objets fragiles ou déplacer des charges lourdes.
À l’avenir, nous pouvons nous attendre à un développement plus poussé des systèmes sensoriels des robots. Cela leur permettra de mieux percevoir l’environnement environnant, d’interagir avec lui et de s’adapter indépendamment à de nouvelles tâches sans configuration manuelle.
Plateforme d’intelligence artificielle industrielle
Plus de cent billions de dollars représente la valeur de l’infrastructure vieillissante dans le monde entier. Et cet objet colossal est sous une pression toujours croissante. Les perturbations de la chaîne d’approvisionnement, les pénuries aiguës de main-d’œuvre qualifiée et les menaces de sécurité en constante évolution créent d’énormes risques pour l’économie mondiale.
Avathon a développé une plateforme révolutionnaire d’intelligence artificielle industrielle. La plateforme unit des ensembles de données disparates et leur superpose des informations contextuelles. Elle crée ainsi une vue d’ensemble complète des opérations. Les composants clés de la technologie sont les jumeaux numériques – des copies virtuelles d’actifs physiques qui permettent de surveiller, simuler et optimiser le fonctionnement des équipements en temps réel. Les modèles d’intelligence artificielle préentraînés couvrent la maintenance prédictive, la détection d’anomalies et l’optimisation des processus.
Selon des études internationales, les temps d’arrêt non planifiés d’équipements critiques coûtent aux entreprises des milliards de dollars annuellement. La plupart des entreprises n’utilisent qu’une petite partie des données qu’elles collectent. Elles manquent d’énormes opportunités d’optimisation. Les méthodes traditionnelles de maintenance et de gestion des actifs s’avèrent inefficaces dans des conditions de complexité croissante des systèmes industriels.
La plateforme Avathon permet de maximiser la disponibilité des actifs à forte intensité de capital. C’est d’une importance critique pour les entreprises avec des équipements coûteux. Pour les entreprises manufacturières, la plateforme fournit un renforcement efficace des capacités en optimisant les processus et en augmentant la productivité. Une attention particulière est accordée à la sécurité des travailleurs dans des conditions industrielles. Les modèles prédictifs identifient à l’avance les situations potentiellement dangereuses. La capacité à déployer des applications à grande échelle, sur divers appareils, localement ou dans le cloud, avec une configuration minimale, rend la solution flexible et adaptative à différents scénarios d’utilisation. En fin de compte, la plateforme Avathon aide les entreprises non seulement à résoudre les tâches actuelles, mais aussi à se préparer pour l’avenir de la production autonome et des villes intelligentes.
À l’avenir, nous pouvons nous attendre à une intégration encore plus profonde des différents composants de la plateforme. Les jumeaux numériques, les modèles prédictifs et les systèmes de prise de décision fonctionneront comme un seul organisme. À mesure que l’intelligence artificielle devient plus sophistiquée, nous pouvons également nous attendre à l’émergence de systèmes capables non seulement de prédire et de prévenir les problèmes, mais aussi d’optimiser indépendamment les processus, trouvant des solutions inaccessibles même aux ingénieurs expérimentés.
Équipement technologique en production
Actuellement, la création de pièces métalliques pour avions, voitures ou satellites prend des mois en raison de la nécessité de fabriquer des outillages et des matrices coûteux. L’équipement technologique en production est un ensemble de divers outils et dispositifs nécessaires pour l’installation, le mouvement, le traitement, la mesure et l’emballage dans la fabrication de produits. Il comprend divers éléments : moules, dispositifs de soudage, appareils de traitement par machine et bien plus encore.
Machina Labs a développé une solution révolutionnaire : la plateforme RoboCraftsman, qui combine les réalisations en robotique et en intelligence artificielle pour créer une fabrication de nouvelle génération. La technologie est basée sur le processus RoboForming – utilisant des robots industriels avec sept degrés de liberté pour former progressivement des tôles en pièces complexes sans matrices et moules traditionnels. Le système utilise l’intelligence artificielle et l’apprentissage automatique pour contrôler le processus de formage en temps réel. Il s’adapte aux caractéristiques du matériau et à la géométrie de la pièce. Les robots travaillent comme de vrais maîtres artisans, mais avec la précision et la répétabilité de la fabrication moderne.
Selon les recherches industrielles, jusqu’à soixante-dix pour cent du temps dans la fabrication traditionnelle est consacré non au processus de fabrication lui-même, mais à la préparation des outils et des équipements. Pour de nombreuses entreprises, le coût des matrices peut atteindre des centaines de milliers de dollars. Cela rend la production en petites séries économiquement irréalisable. Même des modifications mineures à la conception des pièces nécessitent souvent un outillage complet. Cela ralentit de manière critique le processus de développement et de test de nouveaux produits. Ces retards peuvent coûter aux entreprises des millions de dollars en bénéfices perdus. Les méthodes traditionnelles de traitement des tôles sont essentiellement restées inchangées pendant des décennies. Cela limite les capacités des ingénieurs et des concepteurs avec des processus technologiques obsolètes.
La plateforme RoboCraftsman peut instantanément changer d’outils et de capteurs pour effectuer diverses opérations. Cela inclut le formage, la numérisation, la découpe et le perçage d’une large gamme de matériaux. Une caractéristique importante de la technologie est la documentation complète du processus de production de chaque pièce. Toutes les données sont enregistrées sous forme de jumeau numérique contenant l’historique complet de fabrication.
Machina Labs réunit des experts en technologie, matériaux et fabrication provenant d’entreprises leaders. Cela inclut SpaceX, Relativity Space, Novelis, Carbon et Stratasys. Avec la capacité de passer de la conception à la pièce finie en quelques jours plutôt qu’en mois, les fabricants peuvent itérer leurs conceptions, mener des tests et mettre en œuvre des innovations plus rapidement. La technologie de traitement sans matrices rend économiquement viable la production en petites séries de pièces qui étaient auparavant non rentables avec l’estampage traditionnel. Pour les fabricants de matériaux composites, RoboForming réduit considérablement le temps de préparation de la production, diminue la durée du cycle et réduit les déchets de matériaux. La compatibilité avec les métaux à haute température avec de faibles coefficients de dilatation thermique, comme l’invar, permet la fabrication rapide de grandes surfaces aérospatiales de précision. Machina Labs propose deux façons d’accéder à leurs plateformes de fabrication : vous pouvez louer du temps de production sur leurs cellules RoboCraftsman internes ou acheter la plateforme dans le cadre d’un accord à long terme.
Nous verrons probablement bientôt une intégration plus étroite avec les systèmes de conception. Les changements de conception se traduiront automatiquement en changements dans le processus de production. Une direction intéressante pourrait être le développement de systèmes RoboCraftsman plus compacts et mobiles qui pourraient être déployés directement sur le site d’utilisation du produit, par exemple, dans des missions spatiales.
Que pensez-vous de l’avenir de la fabrication flexible basée sur la robotique et l’intelligence artificielle ? Je me demande si les entreprises sont généralement prêtes à mettre en œuvre des technologies de traitement des métaux sans matrices.
Résolution des problèmes de l’industrie alimentaire
Dans l’industrie alimentaire, les entreprises font face à une crise de main-d’œuvre sans précédent. Selon les dernières données, aux États-Unis seulement, il y a plus d’un million cent mille postes vacants dans la préparation alimentaire. D’ici deux mille trente, ce nombre pourrait atteindre trois millions.
Chef a développé un système d’automatisation robotique révolutionnaire utilisant les avancées de l’intelligence artificielle pour résoudre les problèmes de l’industrie alimentaire. Au cœur de la technologie se trouve le système d’exploitation ChefOS – le modèle de manipulation alimentaire le plus intelligent du monde. Ce système fait pour le monde physique ce que ChatGPT a fait pour le langage. Si GPT prédit le prochain mot dans une séquence, alors le modèle généralisé de manipulation alimentaire sait quelle action robotique devrait suivre ensuite dans le monde réel.
Les robots Chef utilisent la vision par ordinateur et l’apprentissage profond pour travailler dynamiquement avec les produits. Ils considèrent les propriétés spécifiques des ingrédients, la topographie des plateaux et les spécificités de la préparation alimentaire un jour particulier. Le système peut suivre les plateaux se déplaçant le long du convoyeur et placer précisément les produits dans les bons compartiments. Une caractéristique importante de la technologie est l’apprentissage continu. Plus les robots effectuent d’opérations, meilleur devient le système. Les robots Chef ont déjà effectué des centaines de milliers d’opérations avec divers ingrédients dans des conditions de production réelles. Chacune de ces opérations enrichit les données d’entraînement, rendant le système encore plus fiable et flexible.
L’entreprise fonctionne sur un modèle de “Robotique en tant que service”. Cela réduit considérablement la barrière d’entrée pour la mise en œuvre de l’automatisation. L’avantage concurrentiel de l’entreprise est basé sur l’énorme quantité de données collectées à partir de la production réelle. Cela permet à leurs modèles d’intelligence artificielle d’exceller dans la gestion de la grande variabilité des produits alimentaires.
La mise en œuvre des solutions Chef apporte de nombreux avantages aux entreprises alimentaires. Cela commence par des économies de coûts dès la première année d’utilisation. Le système augmente considérablement les volumes de production, augmente le rendement des produits et réduit les déchets. Grâce à la capacité de travailler avec des ingrédients divers, des tailles de portions et des conteneurs variés, les robots Chef assurent une haute cohérence et un rendement de produits même dans les productions avec de grands assortiments. La taille compacte du système, comparable à un espace de travail humain, permet d’intégrer des robots sans restructuration complexe de la ligne de production. Il suffit de les connecter à l’électricité, à l’air comprimé et au Wi-Fi. Les robots sont conçus pour un fonctionnement sûr près des humains conformément aux normes. Cela permet une automatisation partielle de la ligne où les personnes et les robots travaillent côte à côte. Le système se distingue par sa facilité d’utilisation – un responsable de ligne peut le configurer en quelques minutes, et le changement de produit ne prend que cinq minutes.
Amélioration de la sécurité du personnel dans des conditions industrielles
Imaginez un travailleur grimpant sur un poteau électrique dans une zone mal éclairée. Ou un mineur descendant profondément sous terre où la communication est pratiquement absente. Quotidiennement, des millions de personnes risquent leur vie en effectuant des travaux dangereux dans l’industrie, la construction, l’exploitation minière et la logistique.
Proxgy a développé une gamme unique d’appareils IoT portables pour améliorer la sécurité et l’efficacité du travail du personnel dans des conditions industrielles. Leur produit phare est SmartHat. Ce n’est pas seulement un casque de protection, mais un écosystème intelligent à part entière qui combine de nombreuses fonctions en un seul appareil. Le casque est équipé d’une double caméra avec un capteur infrarouge pour la prise de vue en faible luminosité et une caméra arrière avec un angle de vue de cent soixante degrés. Il offre un contrôle visuel complet de l’environnement de travail. La radio intégrée élimine le besoin de transporter un appareil encombrant supplémentaire. Un bouton d’appel d’urgence SOS envoie instantanément un signal au siège lorsqu’une situation dangereuse survient. Une attention particulière est accordée à la sécurité de l’appareil lui-même. La technologie brevetée de prévention d’explosion de batterie garantit que le casque ne deviendra pas une source de danger supplémentaire. SmartHat est également équipé d’un ensemble complet de capteurs pour surveiller l’état humain : détection de chute, contrôle du port du casque, suivi des dangers tels que la détection de fuites de gaz ou le géofencing, et surveillance de l’environnement pour la température, l’humidité et le niveau de bruit.
Selon l’Organisation internationale du travail, plus de deux millions d’accidents mortels se produisent annuellement sur les lieux de travail. Les pertes économiques dues aux accidents du travail et aux maladies atteignent quatre pour cent du PIB mondial. Les travailleurs particulièrement vulnérables sont ceux qui effectuent des tâches seuls, lorsque personne ne peut fournir une assistance immédiate en cas d’urgence. Malgré la numérisation de nombreux aspects de la production, les outils de protection et de surveillance de l’état des travailleurs eux-mêmes restent étonnamment primitifs et inefficaces.
La mise en œuvre des produits Proxgy apporte des avantages significatifs tant pour les travailleurs que pour les organisations. Pour les employés individuels, c’est principalement une augmentation de la sécurité personnelle. Les appareils peuvent détecter des situations dangereuses, suivre les signes vitaux et fournir une communication immédiate en cas d’urgence. Les LED intégrées améliorent considérablement la visibilité dans les endroits mal éclairés. La fonction de surveillance de l’emplacement est particulièrement précieuse pour les travailleurs effectuant des tâches seuls. Pour les entreprises, les produits Proxgy offrent la possibilité de surveillance à distance et d’inspections via les caméras des appareils. Cela économise du temps et des ressources, surtout dans des situations où la présence physique est difficile ou dangereuse. La capacité à suivre l’état des travailleurs permet de prévenir les risques liés à la santé. La durabilité et la fiabilité des appareils assurent leur fonctionnement réussi même lors de l’exécution de tâches complexes comme l’escalade de poteaux ou le travail avec des outils lourds.
À l’avenir, nous pouvons nous attendre à une intégration encore plus étroite de l’intelligence artificielle pour prédire les situations potentiellement dangereuses avant qu’elles ne se produisent, en se basant sur des données historiques et des modèles. Une direction intéressante pourrait être la création d’un écosystème d’appareils interagissant, où des casques intelligents, des gants, des chaussures et d’autres éléments d’équipement de protection échangeront des données, créant une image complète de l’état du travailleur et de l’environnement.
Analyse de cent pour cent du temps de conduite
Selon les recherches industrielles, environ quatre-vingt-dix pour cent des accidents de la circulation routière impliquant des transports commerciaux se produisent en raison de facteurs humains. Chaque incident de ce type coûte aux entreprises en moyenne cinquante mille dollars en dépenses directes, sans compter les pertes indirectes dues à l’immobilisation des équipements et aux dommages de réputation.
Netradyne a développé le système révolutionnaire Driver•i, qui utilise des technologies avancées de vision par ordinateur et de calcul en périphérie pour analyser chaque minute de conduite. Contrairement aux enregistreurs traditionnels qui s’activent uniquement lors d’événements critiques, Driver•i analyse cent pour cent du temps de conduite. Cela permet non seulement d’identifier les comportements risqués mais aussi de noter les actions positives des conducteurs.
Le roulement parmi les conducteurs professionnels est très élevé. Chaque conducteur perdu signifie des dépenses supplémentaires pour trouver et former un nouvel employé. Les systèmes de surveillance traditionnels basés sur l’enregistrement uniquement des incidents critiques créent une attitude négative envers le contrôle de la part des conducteurs. Ils perçoivent les caméras comme un outil de punition plutôt que d’aide. La plupart des entreprises sont contraintes d’utiliser des solutions disparates pour assurer la sécurité, la conformité réglementaire et la gestion de flotte. Cela conduit à l’inefficacité et à la perte de données précieuses.
Au cœur du système Driver•i se trouve l’intelligence artificielle qui reconnaît les objets et applique des algorithmes d’apprentissage automatique pour déterminer les relations de cause à effet des événements. Elle utilise l’enregistrement vidéo comme preuve. Le système d’évaluation unique GreenZone Score, basé sur des principes de renforcement positif et de coaching, aide les flottes à réduire les comportements de conduite risqués et à améliorer la sécurité des conducteurs. Driver•i fournit des avertissements en temps réel directement dans la cabine. Il offre une vue panoramique à trois cent soixante degrés, ce qui réduit considérablement le nombre de collisions et augmente le pourcentage d’exonérations de conducteurs dans des situations litigieuses. La version la plus récente du système, Driver•i One, combine les capacités de surveillance vidéo avec des applications pour la conformité réglementaire.
La mise en œuvre du système Driver•i apporte des avantages significatifs tant pour les conducteurs eux-mêmes que pour les entreprises. Les conducteurs reçoivent des commentaires constructifs qui stimulent un comportement positif et aident à améliorer les indicateurs dans le système d’évaluation GreenZone Score. Il est important de noter que le système est perçu par les conducteurs non comme un outil de surveillance mais comme un assistant, comme en témoignent de nombreux avis. Comme l’a souligné Dennis Davis, directeur de la sécurité chez Prime : “Nous avons vu certains conducteurs qui étaient initialement critiques à l’égard de la solution et qui menaçaient même de quitter complètement l’entreprise changer d’avis.” Pour les entreprises, le système fournit une réduction significative des accidents, comme le confirme John Elliott, PDG de Load One Transportation & Logistics : “Il ne fait aucun doute que nous pouvons examiner les taux d’accidents avant et après l’installation des caméras et voir une corrélation directe dans la réduction du nombre d’accidents et d’incidents. Nous avons commencé à voir des changements cardinaux dans les chiffres après seulement quelques mois.” De plus, Driver•i One simplifie la conformité aux exigences réglementaires pour la comptabilisation du temps de travail des conducteurs, les rapports d’inspection des véhicules et l’Accord international sur la taxe sur les carburants. Il élimine le besoin d’appareils de journalisation électroniques séparés.
Automatisation des opérations logistiques
Selon les recherches industrielles, jusqu’à soixante-dix pour cent des coûts opérationnels des entreprises logistiques proviennent du travail manuel lié à la manipulation des marchandises. Pendant ce temps, l’industrie fait face à une pénurie chronique de personnel. Aux États-Unis seulement, la pénurie de travailleurs d’entrepôt dépasse un demi-million de personnes. Ce chiffre double pendant les saisons de pointe.
Dexterity a développé sa propre approche pour automatiser les opérations logistiques basée sur le concept d'”intelligence artificielle physique” – une technologie qui dote les robots d’une dextérité et d’une adaptabilité semblables à celles des humains. Au cœur de la solution de Dexterity se trouvent des mécanismes industriels que l’entreprise appelle “superhumanoïdes”. Ce sont des robots capables de se déplacer plus rapidement, d’atteindre plus loin, de soulever plus lourd et de travailler infiniment plus longtemps que les humains. Ces mécanismes impressionnent par leurs caractéristiques : capacité de levage jusqu’à soixante kilogrammes, portée du manipulateur de plus de cinq mètres, opérabilité à des températures de zéro à cinquante degrés Celsius, à des altitudes jusqu’à un kilomètre et demi, et à une humidité jusqu’à quatre-vingt-dix pour cent.
Le roulement du personnel d’entrepôt atteint cent vingt pour cent par an. Cela signifie un renouvellement complet du personnel et des coûts supplémentaires pour l’embauche et la formation. Les solutions d’automatisation traditionnelles telles que les systèmes de convoyeurs ou les manipulateurs robotiques rigides ne peuvent pas gérer la diversité des formes, des tailles et des types d’emballage des marchandises modernes. Ces systèmes sont généralement conçus pour travailler avec des articles à paramètres standard et nécessitent des investissements importants dans l’infrastructure et la restructuration des processus existants. En conséquence, de nombreuses opérations logistiques sont encore effectuées manuellement. Cela limite l’échelle des entreprises et augmente les dépenses opérationnelles.
Dexterity utilise des équipes de centaines d’agents d’intelligence artificielle qui fournissent collectivement des indicateurs de production de niveau industriel. Le système Arbiter contrôle strictement l’exécution de l’IA, gérant tous les agents et éliminant les hallucinations d’intelligence artificielle, les erreurs de cas limites et les défaillances aléatoires.
En automatisant les tâches répétitives, les systèmes robotiques de Dexterity permettent de maximiser le potentiel du personnel. Ils permettent aux employés de se concentrer sur un travail plus complexe et cognitif. Un opérateur humain peut gérer dix robots ou plus simultanément. Les capitaines de flotte contrôlent le fonctionnement d’installations ou de réseaux entiers. Dexterity forme le personnel des clients pour les deux rôles. Elle transforme des employés ordinaires en opérateurs hautement qualifiés de systèmes robotiques. Pour les entreprises, les solutions Dexterity fournissent une valeur transformationnelle qui affecte directement les indicateurs financiers. L’entreprise utilise des jumeaux numériques avancés pour modéliser et évaluer l’impact de la mise en œuvre de l’intelligence artificielle physique sur les flux de trésorerie des clients. Chaque solution prend en compte les caractéristiques uniques des problèmes des clients et offre un ensemble complet d’adaptateurs pour configurer les flux de travail de l’entreprise. Une attention particulière est accordée à la sécurité. L’intelligence artificielle physique, les logiciels et le matériel de Dexterity sont orientés vers l’humain. La sécurité prime dans chaque opération de production.
Malgré les capacités impressionnantes des technologies Dexterity, des questions ouvertes demeurent sur leur développement et leur mise en œuvre futurs. Comment l’interaction entre les opérateurs humains et les équipes de robots se développera-t-elle ? À l’avenir, nous pouvons nous attendre à une autonomie encore plus grande des systèmes robotiques. L’intelligence artificielle physique sera capable non seulement d’effectuer des opérations assignées mais aussi d’optimiser indépendamment les processus et de s’adapter à de nouvelles tâches sans reprogrammation.
Conclusion
L’intelligence artificielle dans l’industrie crée la fondation de la quatrième révolution industrielle. Elle change radicalement les processus de production, de la conception à la livraison du produit final.
Pour les travailleurs, cela signifie passer du travail physique à la gestion de systèmes intelligents. Pour les consommateurs, cela signifie des produits de meilleure qualité et plus abordables. Avec le temps, nous verrons des usines entièrement autonomes où l’intelligence artificielle coordonne l’ensemble du cycle de production.